My father and I bought a Crescent 465. We wanted a small, portable boat for fishing and short trips in the lakes and sea nearby. We settled for the 465 model because it is sturdy enough and good value for the money. So we scanned the market on second hand 465’s and found one that we liked.
Today, I know what we did wrong. Usually we don’t dive into matters without precautions and don’t ask me why we did it this time. Eager at best, but pretty stupid when given enough time to think.
First we should have searched the net for problems on the Crescent 465. If you google the model along with the word “problem”, you know what I talk about. We surely aren’t the first ones to encounter this.
But here we are. Proud owners of a Crescent 465!!!
All the woodwork in the boat was thoroughly rotten. Wich in turn made the boat unstable and a potential hazard to use in water. Everything had to be changed.
So. You have been warned. Do your homework before buying a 465 or you’ll end up doing this:
First, cut away all the rotten wood. We used a grinder to carefully cut out the interior as close to the hull as possible. Careful not to damage the hull itself.
We also decided to reuse the cut out parts as much as possible. So we removed them as intact as possible.
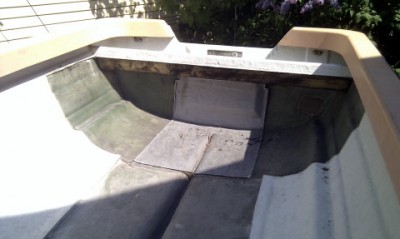

We used an axe, a sledge hammer and a small crowbar to break away the residual edges. It worked extreamly well and was very efficient.
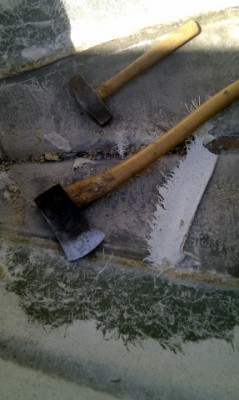
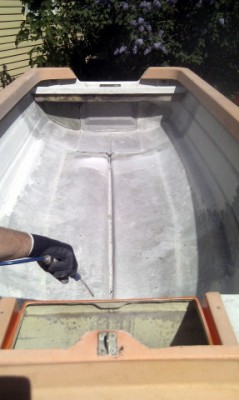
Then, we made a new floor (durk in Swedish) from polyester, fibreglass and divinycell. We put two layers of polyester and fibreglass on each side.
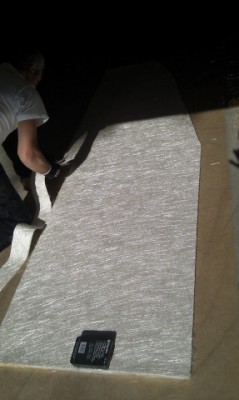
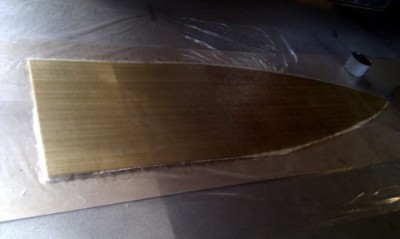
We grinded away all the rotten plywood that was inside the benches and put new layers of fibreglass and polyester inside. The upper part of the benches where reinforced with 10mm divinycell creating a sandwich construction. We hope it will be strong enough.

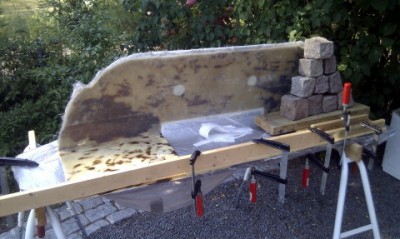
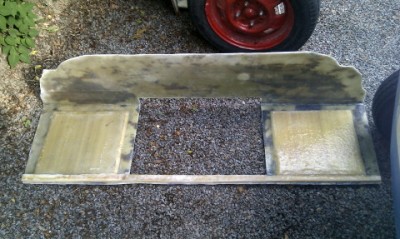
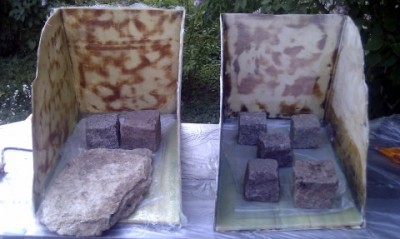
We made supports on the underside of the floor to help carry the weight and help in keeping the floor attached to the hull. We straighted up the hull carefully before fastening the floor. Without the floor the hull is pretty easy to bend and skew.
Then we fastened the floor with sikaflex. Sikaflex is a polyuretan glue with superb adhesive. The marine variant is resist to water.

We made a light weight filler from polyester and micro glass balloons. We used the filler to smooth out all gaps.
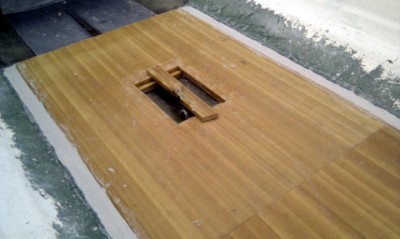
When the floor was in place all other interior was laminated in. Almost all wood is now removed from the construction and very little can rot. Everything is made using the sandwich technique with fibreglass, polyester and divinycell.
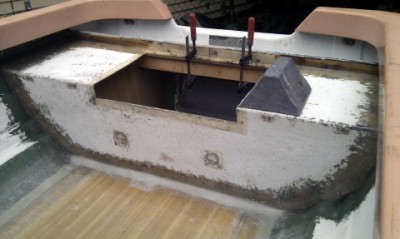

Finally we topcoated the interior. We where surprised on the final finish and look. The topcoat was incredibly forgiving in covering minor errors and gave a very professional look.
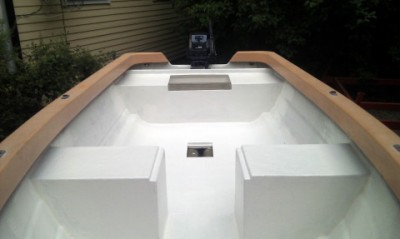
Last but not least we attached the hatches and put new locks on them. Voila!
We put a lot of time in this project. Far more time and money was spent in repairing this boat than we could ever have believed from the beginnig. But this is still a rather cheap way of getting a boat. Looking back we are pleased with the experience of laminating in polyester. It is easy to get the hang of it and if you don’t achieve what you want the first time, cut away and redo until you are satisfied with the result. Good luck!